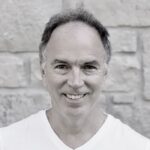
Jim ‘Slim’ Mimlitz, SCADAmetrics
Many factories feature paint and heat-curing operations, which consume massive amounts of natural gas. Utilizing the tools at its disposal, the modern factory can measure — and optimize — its natural gas consumption within the context of an Allen-Bradley-based FactoryTalk/PLC Ethernet network or Modbus/TCP network.
In order to achieve the monitoring goals, each natural gas consumption point should be equipped with a gas meter, such as a Rotary Gas Meter with solid-state pulse output. The pulse signal is then connected to an EtherMeter, which is networked into the plant’s control Ethernet. Common rotary gas meter brands include GE® Dresser®/Roots®, Romet®, Elster®/American®, and others.
SCADAmetrics TV Video Illustration: EtherMeter and Rotary Gas Meter.
Each EtherMeter processes the pulses and converts them into real-world measurable quantities: totalization (total cubic feet), and instantaneous rate-of-flow (cubic feet per hour). The EtherMeter has the capability of processing one or two gas meters.
On an Allen-Bradley-based Ethernet network, the EtherMeter emulates a MicroLogix 1100 PLC, so integration into FactoryTalk is a snap. Data requests are formulated as SLC500 EtherNet/IP message instructions — basically as scanning a range of N-registers. If the control network is based upon Modbus/TCP, then data requests are formed as familiar 40,00x register requests.
Are you interested in learning how the EtherMeter can help your factory sub-meter it’s natural gas, water, and electricity usage? Give us a call… We’ll be glad to help!